The magneto test set-up is making some progress, albeit slowly. For the spark plug rack, I got all six candles mounted, using grey motor BP5S plugs. Remember that I need a huge gap, around 0.3125”, to overcome the fact that we are testing at atmospheric pressure. The BP5S plug gap won’t open that far… in fact, even if you grind away all of the earth electrode the biggest gap you can get is 0.175” (this is where the centre electrode arcs to the threaded portion of the sparkplug). To overcome this, I threaded the plugs into the rack, then die-ground the threaded portion back to expose the (insulated) centre electrode – see photo below:
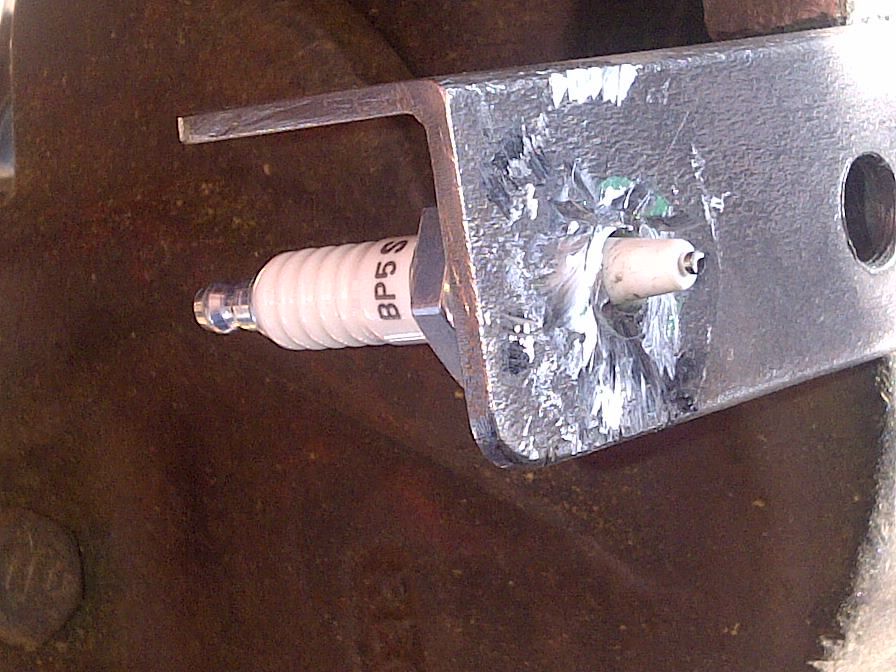
With this setup, the distance from the uninsulated portion of the centre electrode to the rack is 0.37”. If I don’t supply some other form of earth elecrode, the centre electrode will arc the 0.37” distance back to the rack (i.e. the maximum plug gap with this setup is 0.37”, more than the 0.3125” that I need). To make the plug gap adjustable, I made a rack of earth electrodes. The earth electrodes are made from gutter bolts (love those wing nuts), with the tips ground to a point. By adjusting them up and down I will be able to set the gap accurately on each plug.
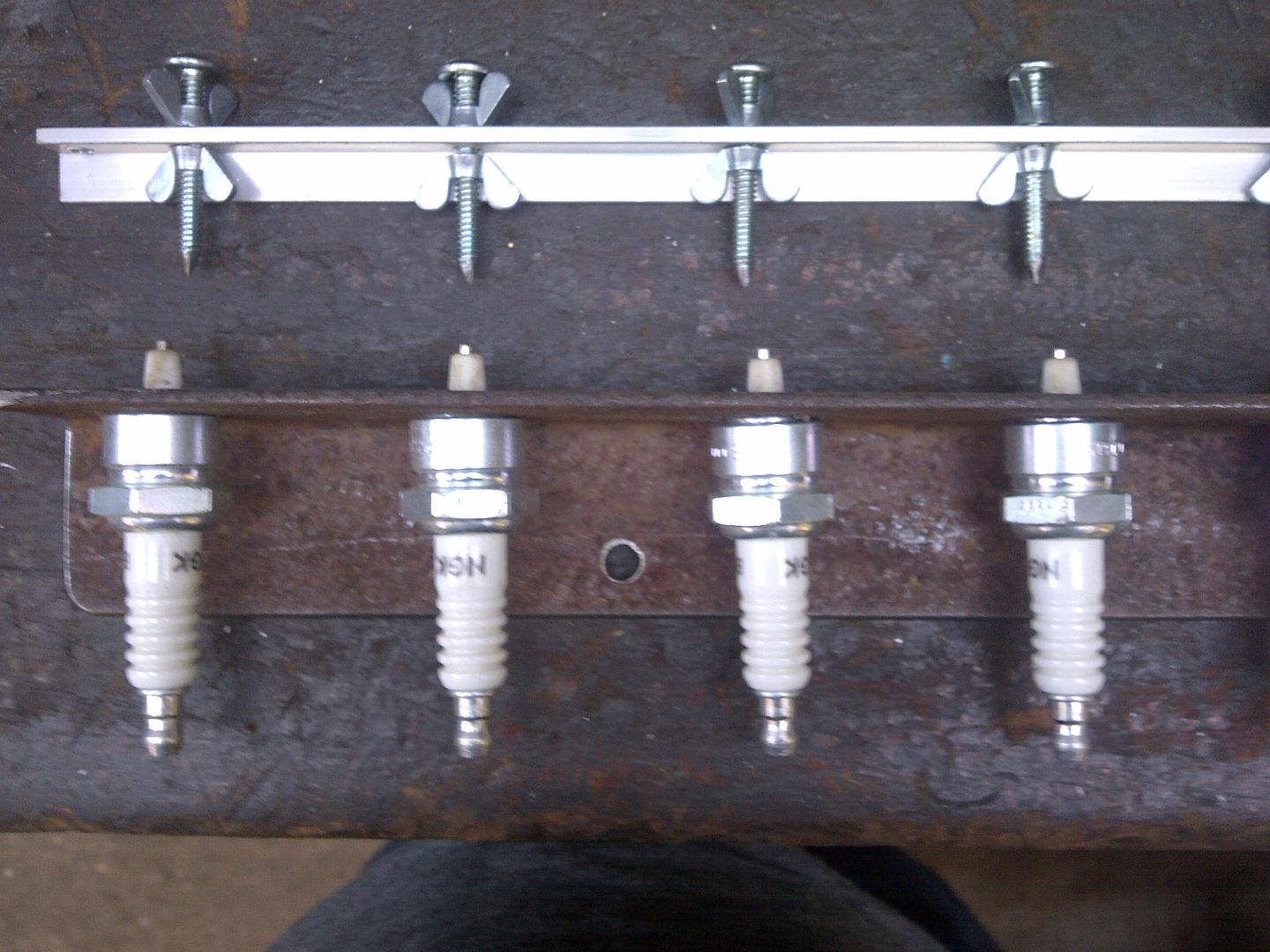
I also received the drive gear and spindle, which has been turned down from a grey motor camshaft (many thanks again Mr Brown).
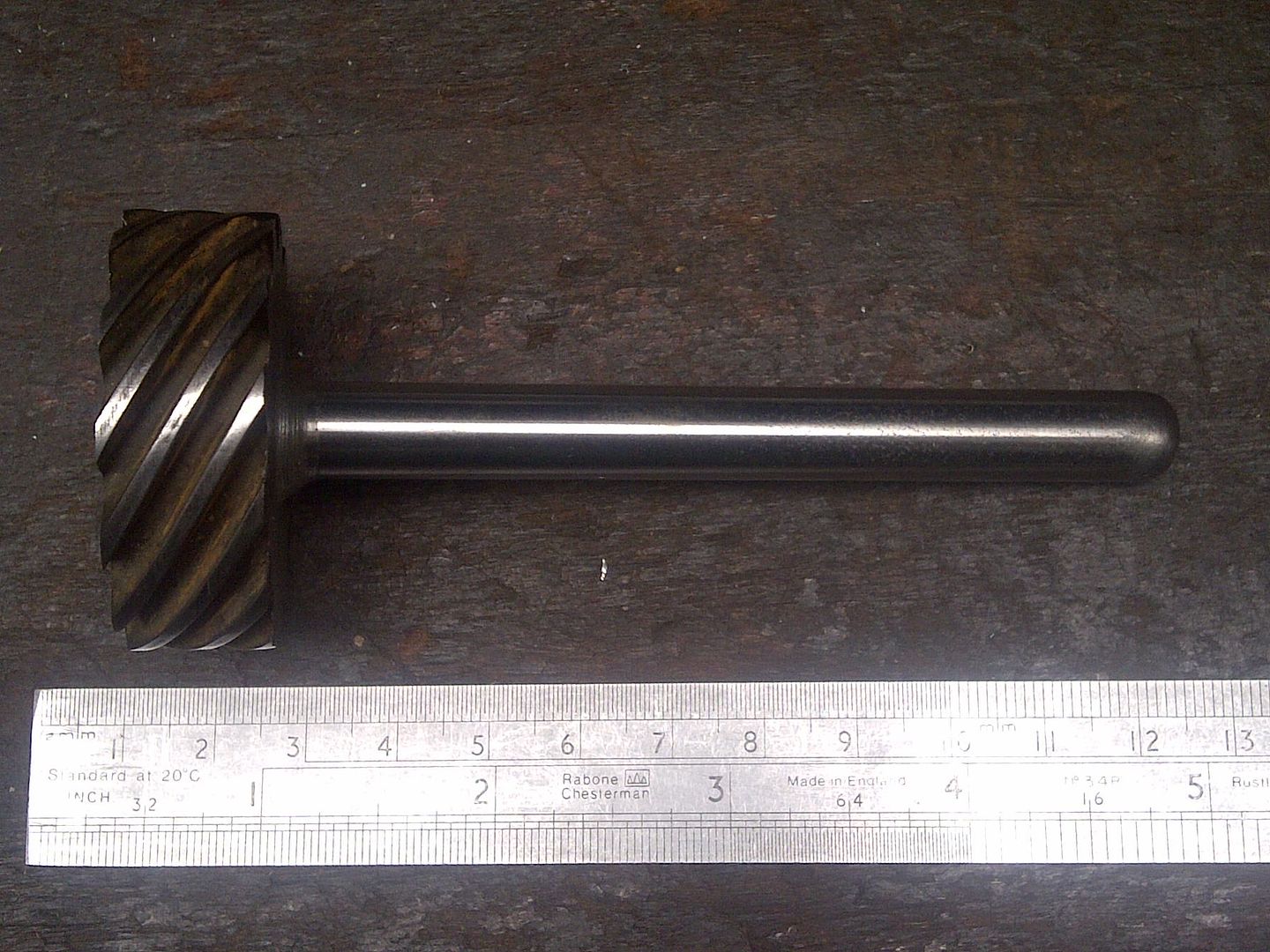
Mounting this in my drill press, I’ve been able to dummy up some brackets, and have successfully spun a grey motor dizzy. The bracketry needs a bit more work, but for now I’m happy – I’ve got a 16 speed dizzy/magneto tester

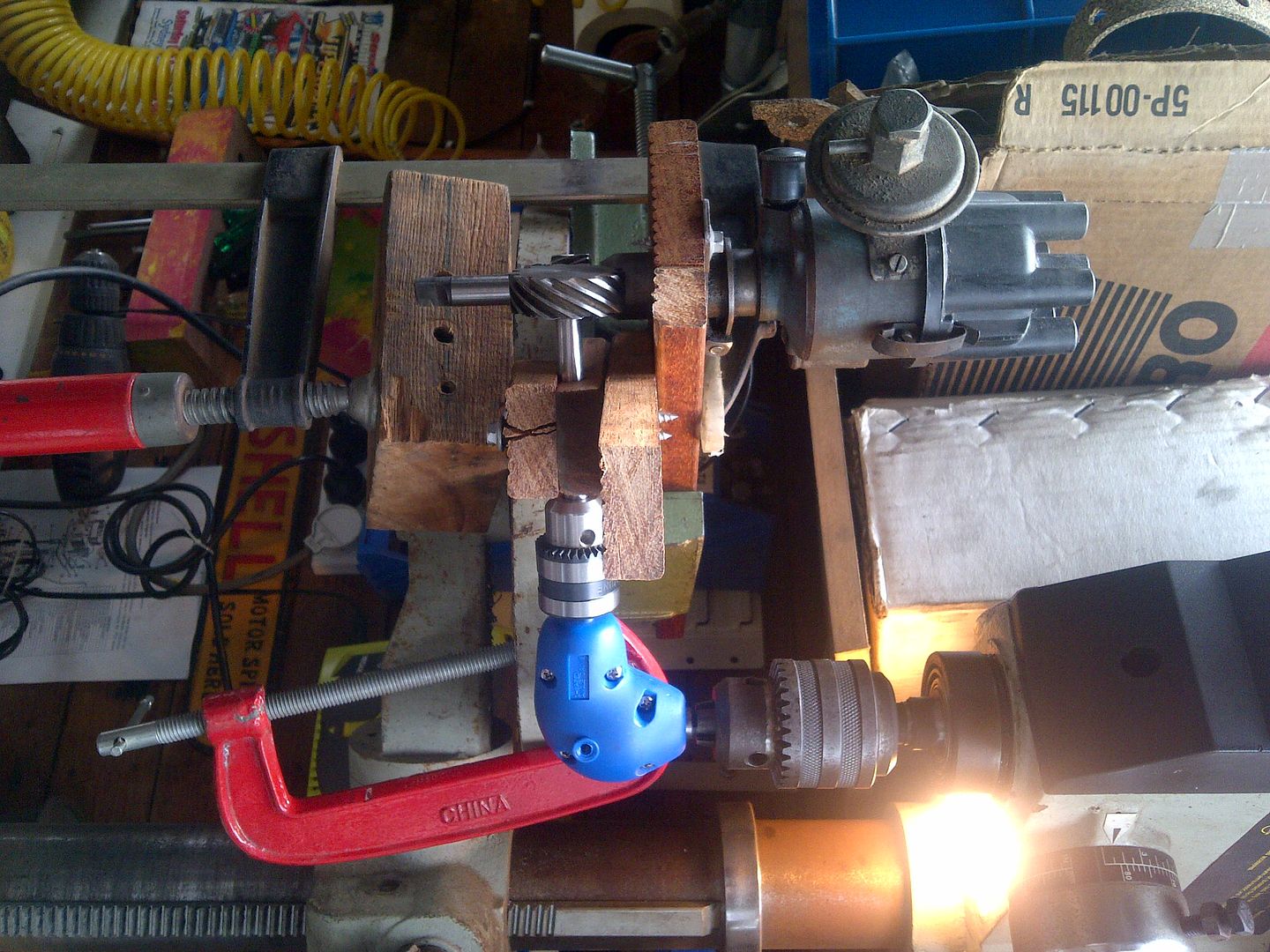
Not the best photo in the world, and sideways but you get the idea.
On the oscilloscope front, I’ve bought some test probes, which turned into a pretty major drama for something so simple. The store initially had none, and had to order them in. They arrived… and were two different probes (they need to be identical to assist in calibrating the oscilloscope channels, especially as I don’t have any calibration tools). The store was pretty good about it, and ended up mailing two identical probes to me. I’ve still got some learning to do (sadly my oscilloscope training material, purchased from the US, disappeared in the post… hopefully the resent materials get to me soon).
On the positive side (and after Mr Brown reminded me), I did get my tin-foil hat made. The purple loop keeps the Zim Pirates away…
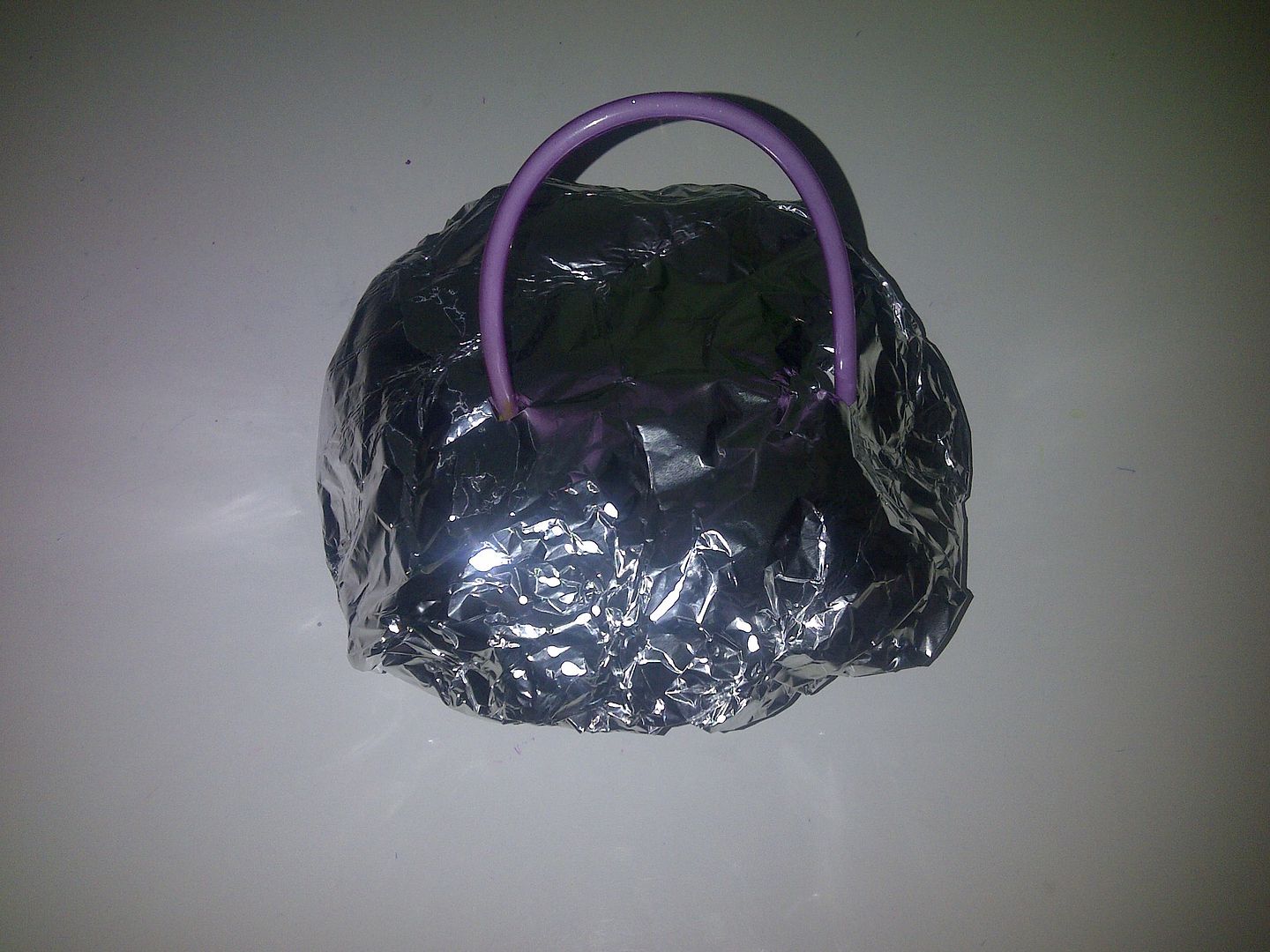
Just gotta work out the lightning rod for the shed.
Cheers,
Dr Frankenharv.